Productivity is a key factor in any production process—whether in a laboratory, research center, food company, or training facility. Maximizing efficiency and output not only allows you to produce more in less time, but also helps optimize resources and reduce costs.
After selling thousands of autoclaves around the world, we’ve observed and collected a wide range of strategies that our customers regularly implement to improve their productivity.
In this article, we’ll explore several effective practices that can make a real difference in any work environment involved in food canning production.
1. Optimizing production capacity
One of the first steps to boosting productivity is making the most of the available space, ensuring that each cycle processes as many product units as possible.
When it comes to autoclaves, production capacity can be optimized in two key ways:
- Choosing the right container size: Carefully selecting the dimensions of your packaged product helps maximize the use of space inside the autoclave, increasing process efficiency.
- Adjusting internal layout: Using baskets or trays with the appropriate height allows you to fit more units per cycle without compromising the quality of the thermal treatment.
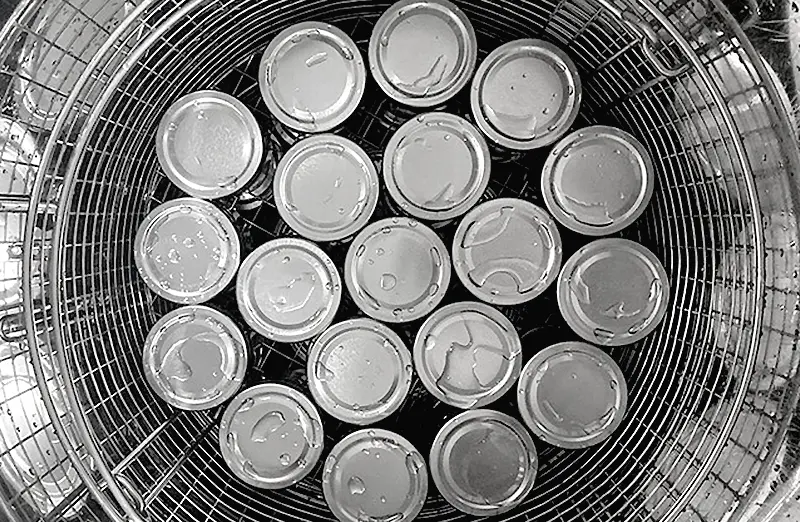
Conducting a container-specific productivity study is essential to determine the best possible configuration and avoid wasted space.
For clients working with cylindrical containers, we’ve developed an online calculator that lets you automatically calculate production capacity as many times as needed.
For those using non-cylindrical containers, our team of engineers provides personalized productivity studies based on the type and size of the container. Contact us to receive a detailed, free analysis tailored to your specific application.
2. Strategic use of time
Time is a valuable resource in any production process, and managing it efficiently can have a significant impact on overall productivity. Here are some key strategies:
- Scheduling overnight cycles: If your equipment, product, and environment allow it, running cycles at night can effectively add an extra shift without requiring constant supervision—maximizing available time.
- Reducing processing time: Fine-tuning the temperature and duration of each cycle helps strike the right balance between quality and efficiency. In many cases, slightly increasing the temperature can reduce processing time without affecting product quality.
- Optimizing the cooling phase: Cooling is a critical stage in productivity. Implementing methods such as cold water or efficient cooling systems can significantly cut down wait times before handling the products, helping speed up production flow.
3. Integrating cooking segments
An advanced strategy to boost productivity involves combining multiple steps of the process into a single cycle.
In the food industry, some producers take advantage of the heat generated by the autoclave not only to sterilize, but also to cook the product. This reduces the need for additional equipment, shortens prep time, and improves overall operational efficiency.
This technique is especially useful for products like sauces, stews, and meats, where the heat from the autoclave completes the cooking process while ensuring microbiological safety.
4. Automation and the right equipment
Investing in the right technology and accessories can make a big difference in productivity—streamlining processes and reducing the margin for error. Some key strategies include:
- Use of probes and sensors: Monitoring the process in real time allows for automatic parameter adjustments, improving both precision and efficiency. We always recommend using core temperature probes and F0/P0 control—except for highly experienced users.
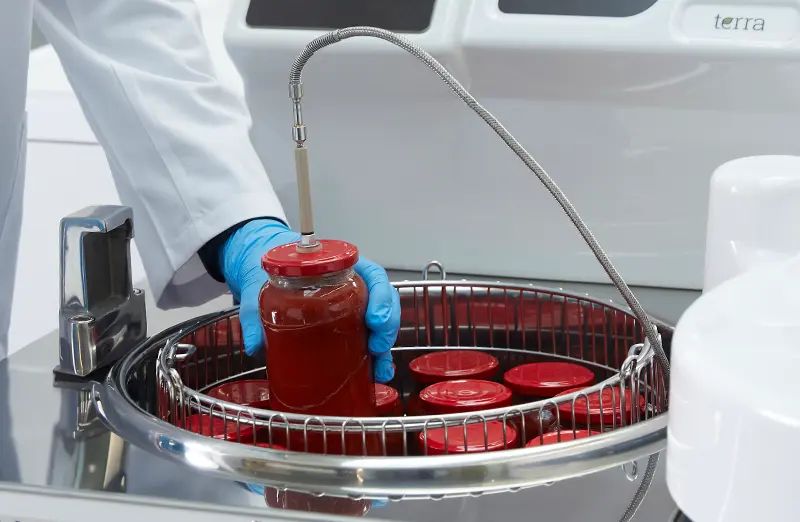
- High-powered equipment: In some cases, choosing high-powered versions of your equipment can significantly reduce heating times and allow more cycles per day. The exact time savings depend on the model, but equipping a unit with more powerful heating elements can shorten the heating phase by 20% to 50%.
- Additional basket sets: Having preloaded baskets ready for processing helps speed up operations by minimizing loading and unloading time between cycles.
5. Implementing good production practices
Beyond equipment and process organization, staff training and the implementation of good practices play a key role in overall productivity. Some essential practices include:
- Process standardization: Documenting procedures and establishing clear parameters helps reduce variability, improve efficiency, and ensure consistent product quality.
- Staff training: A well-trained team works more efficiently and makes fewer mistakes.
- Preventive maintenance: Keeping equipment in optimal condition reduces unexpected downtime and prevents production failures, ensuring a continuous workflow.
Conclusion
Improving productivity in the food canning industry isn’t just about working faster—it’s about working smarter.
Optimizing space usage, reducing unnecessary time, integrating processes, and using the right technology are essential to boosting efficiency in any operation.
By implementing these strategies, you can increase output without needing more resources, resulting in greater profitability and competitiveness.
At Terra Food-Tech®, we’re here to help you optimize your processes and take your production to the next level.
Our food autoclaves are designed to meet your specific needs, ensuring efficiency, precision, and safety in every production cycle.
Looking to improve your productivity and choose the perfect autoclave for your business?
Contact us today. We’ll gladly help you find the right solution.